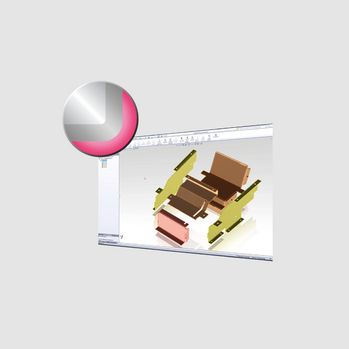
The future is electric: the quality of sheet metal processing meets environmental sustainability, resulting in reduced consumption. The new fully electric automated press brakes of the AMADA EGB series offer added value that aligns with the new Industry 5.0 Transition Plan, an initiative that promotes corporate investments aimed at achieving better energy efficiency in production.
ECONOMIC AND ENVIRONMENTAL BENEFITS
With this new series of press brakes, the use of hydraulic circuits has been abandoned, offering an entirely electric technological solution. An evolution with which AMADA has managed to maintain high bending standards while ensuring significant energy optimization. The implementation of an electric system allows for a considerable reduction in consumption and, consequently, a significant decrease in production costs, resulting in a substantial economic advantage for companies.
FEWER ERRORS AND MORE PRODUCTIVITY
The EGB technology stands out for its extraordinary precision, achieved through the implementation of artificial intelligence in the new AMNC 4ie numerical control system. This system allows for constant and accurate monitoring of the processing, supported by integrated cameras and sensors that promptly detect any anomalies. This solution not only assists the operator but also significantly reduces error margins.
Another innovative element is the revolutionary table movement system, consisting of a servomotor on each side of the electric press brake, unlike traditional configurations, capable of providing both high-speed approach and bending force. This groundbreaking feature not only results in lower consumption costs and higher performance but also ensures productivity and quality, meeting the criteria necessary to initiate the Industry 5.0 process.
SIMPLER AND FASTER PROCESSES
Reducing setup times is crucial in sheet metal bending, as the complexity of tool layouts significantly impacts production costs. AMADA addresses this challenge with the Automatic Tool Changer (ATC), an integrated unit that automates tool configuration, drastically reducing time and costs. Even the most complex setups are completed with precision in record time. This not only lowers costs but also increases the machine's versatility, allowing for quick adaptation to different processes and market trends without losing productivity.
The EGB-1303ATCe uses the updated ATC system, with a 30% greater capacity than the previous model, and introduces several new features aimed at further streamlining the bending process. The lower table incorporates an automatic compensation system operated by servomotors, providing quick adjustments for better-quality processing. The 3-point back gauge system makes part positioning much simpler as one of the support points can be used as a lateral reference; particularly useful for offset, angled, and complex parts.
SUPPORT FOR OPERATORS
A significant innovation is the introduction of applications that simplify the use of the machine, such as the implementation of augmented reality. This system is used for controlling the rear mechanics, allowing the operator to verify the correct position of the piece on a small screen in front of them, instead of directly checking the tools or referring to the numerical control.
The new setup is equipped with the advanced Bi-S II angle measurement system, which is 85% faster than the previous version, and voice control, used to activate certain functions of the press brake or to make program corrections, limiting the need to move around during work and reducing processing times.