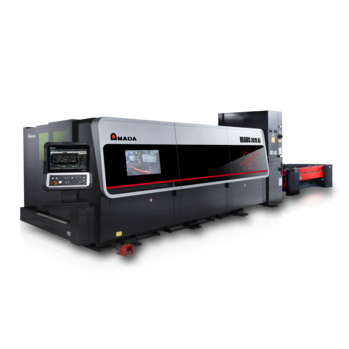
AMADA LASER technologies undoubtedly embody the top of the sheet metal processing industry. Featuring fully developed and produced in-house generators, these systems offer unparalleled added value. The different available functions, customizable according to the models and specific needs of customers, allow optimizing the performance, the productivity and the competitiveness of companies.
ENSIS TECHNOLOGY
The distinctive feature of this AMADA technology lies in its ability to modulate the shape of the laser beam according to the materials and thicknesses being processed. Implemented on all ENSIS-AJ laser machines (3, 6, 9 and 12 kW) and the complete series REGIUS-AJ (6, 9 and 12 kW), this generator is able to automatically adapt and select the optimal laser mode.
AUTO COLLIMATION SYSTEM
We are talking about an innovative solution, integrated with ENSIS technology and characterized by an advanced internal optics system that allows the optimal modulation of the laser beam to adapt it to specific machining needs. This functionality is common to both the ENSIS-AJ range and the REGIUS-AJ series, providing precise and flexible control during the machining process.
REGIUS-AJ, OPTIMIZING PRODUCTION
Equipped with ENSIS generator, the REGIUS-AJ series stands out for its remarkable innovation thanks to the use of linear motors. This feature makes it particularly suitable for working on thin thicknesses or in contexts where frequent axis movements are required. Linear motors allow optimal use of production time, ensuring significant time savings. In addition, the SILKY CUT technology, always associated with REGIUS-AJ machines, helps to improve performance especially in the cutting of medium and high thickness stainless steel, ensuring exceptional cutting quality
PRODUCTIVITY, NOT POWER
With a diverse range of sizes and powers, AMADA machines emerge as the preeminent solution for a variety of laser machining requirements. In an industrial landscape that continues to require increasingly powerful systems, the offer of AMADA laser stands out for its effective productivity optimization. Contrary to the prevailing trend towards high-power machinery, AMADA technologies can give substantial value in terms of operational efficiency. AMADA laser systems, in addition to allowing energy savings, if equipped with the correct automation, are significantly more productive than high-power machines served by pallet change of the competitors. The production capacity does not derive only from the power, but from the correct management of the process.
VENTIS-AJ, THE REVOLUTION OF SINGLE-MODULE LASER
True revolution in sheet metal cutting with VENTIS-AJ technology, AMADA launches the new generation of AMADA laser source machines. Available in models of 4 kW or 6 kW, this series of machines is characterized by its generator consisting of a single module. This innovation allows to increase the quality of the cut even at low power, further optimizing it with the different functions that this technology offers to complete a production performance ideal for all machining.
LBC TECHNOLOGY
LASER INTEGRATION SYSTEM (LIS)
In order to further enhance business performance in the industry, LIS technologies have been introduced that can be integrated on all series of laser cutting machines manufactured by AMADA. These innovations have been specially designed to optimize work quality, greatly simplifying daily operations and minimizing errors in setup, machining and human intervention tasks: